Introduction to Site Progress Inspection
Site progress inspections are a critical component of construction project management. These inspections are paramount for a variety of reasons. Most importantly, they significantly affect cost control, work efficiency, worker safety, and timely project delivery. Through this blog post, we will reveal the ‘key elements in site progress inspection’, acquainting you with its crucial principles and elaborate process. We will uncover the steps ranging from meticulous planning, carrying out, reviewing to adequately documenting the inspection. Furthermore, the granular level analysis will lead us down the path of design specifications, construction materials, and safety protocols amongst others. We will explore how these inspections play a decisive role in managing timelines, budgets, and even in determining the efficacy of subcontractors. So, buckle up and let’s begin this comprehensive exploration into the intricacies of site progress inspection.
The Importance of Site Progress Inspection
Site progress inspection plays a critical role in construction project management by significantly impacting cost, efficiency, worker safety, and project delivery. Not only does it help keep the project budget in check, but it also ensures that the processes being carried out are efficient. Moreover, it also keeps a tab on the safety of the workers, ensuring adherence to rules while identifying and eliminating potential safety hazards. For example, timely inspections can highlight structural issues, providing an opportunity for early rectification, which saves cost and improves safety.
Moreover, site progress inspections play a critical role in determining the project delivery timeline. They provide timely updates about the construction progress, enabling managers to adjust schedules or redistribute resources as needed. For instance, regular checks can indicate if a certain task is taking longer than planned, facilitating early intervention.
Importantly, these inspections underline the crucial necessity for maintaining the quality standard of the project. Regular checks can ensure that the work done aligns with the pre-defined expectations and standards. Thus, site progress inspection is like the control system of a construction project, enabling smoother, safer, and more efficient operations.
Principles of Effective Site Progress Inspection
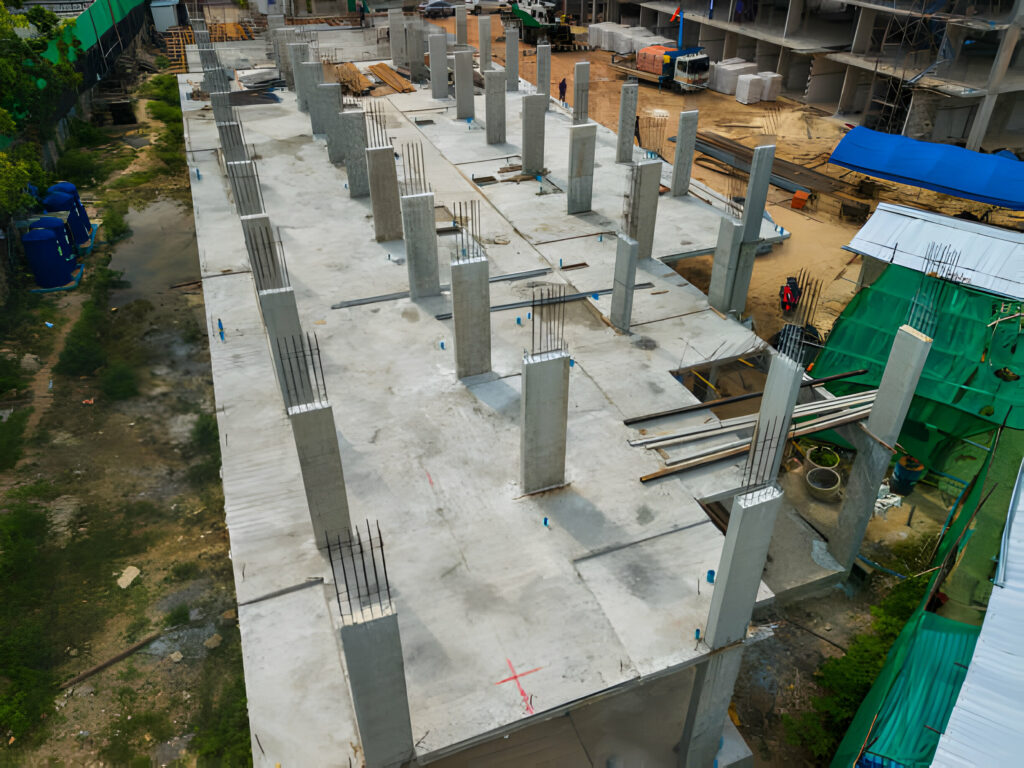
Principles of effective site progress inspection are the compass guiding any successful construction project. Faultless, non-biased inspections constitute the foundation of these principles. To ensure impartiality, an inspector must always be detached from the construction process. It’s advisable that this individual is highly trained and experienced, providing an element of independence when assessing the project’s current status.
The consistency of such checks becomes another pivotal factor. Regularity in conducting inspections allows discernible patterns and trends to arise and lets project managers take timely corrective steps. This methodical approach eradicates any chance of missing out on vital construction details or inconsistencies and aids in prompt problem-solving.
Likewise, the significance of detail orientation in site progress inspections cannot be emphasized enough. From acknowledging the minutest cracks in the concrete to noticing any shocking irregularity in the work practice, an effective inspection leaves no stone unturned. A project manager, for instance, may notice a minor flaw in material usage that, when corrected, enhances structure stability.
Moreover, another principle driving reliable inspections is thoroughness. A cursory glance over a construction site could conceal critical discrepancies. Hence, it’s necessary to invest ample time examining every aspect meticulously – from the use of construction materials to workers’ practices. Consider a scenario where a quick inspection didn’t reveal a scaffolding issue that later led to regrettable delays.
In conclusion, objectivity, regularity, attention to detail and exhaustive site evaluation lay the foundations for effectual site progress inspections. These principles, when adhered to, can exponentially improve the chances of delivering successful and timely construction projects.
How to Conduct a Thorough Site Progress Inspection
Conducting a meticulous site progress inspection involves a sequence of crucial steps. Planning stage sets the course for the process; here, the objective is to identify potential factors that can affect overall project quality, establishing clear inspection criteria based on the project’s specifications. Comprehensive planning should also designate the inspection team and define their roles, ensuring seamless coordination during the process.
The next step involves carrying out the inspection, where the team systematically reviews every facet of the construction site to ensure it aligns with the plan’s pre-set criteria and quality standards. This phase should include close examination of materials used, structural aspects, safety measures, and worker practices. The team conducting the inspection should be trained to remain unbiased and thorough at this stage, accentuating the principle of consistency.
Evaluating the results is another important aspect. Once the inspection is done, the data collected should be interpreted critically. Due to the vast nature of construction projects, appraisal should involve comprehensive analysis, where deviations, if any, are identified. Based on these deviations, necessary amendments should be planned to ensure smooth project progression and high-quality output.
The last step of the process is documenting the inspection. Documentation acts as a record of project progress and can often guide the future course of action, mainly when deviations are found. A detailed document with inspection findings, including pictures or videos serving as visual evidence, can ensure effective communication among teams and stakeholders, thereby increasing the success of measures taken post-inspection.
Exploring the Site Progress Inspection Checklist

A comprehensive exploration of the Site Progress Inspection Checklist serves as a guiding beacon for carrying out meticulous reviews of ongoing construction projects. This checklist encompasses a variety of components that are critical to assessing the health of a construction project. This includes a thorough examination of design specifications, which aids in ensuring that the actual construction aligns with the predetermined plans and all approved modifications. Scrutinizing the types and quality of construction materials used, along with their adherence to the project guidelines, is equally vital. For it plays a prominent role in determining the sustainability, safety, and longevity of the constructed structure.
Further, strict reviews of safety measures form an integral part of the checklist. This component of inspection certifies that all safety regulations are in strict compliance to protect the lives of the labor force, and minimize the chances of accidents and consequent project delays. An evaluation of workers’ practices is another cornerstone of the inspection process, where the best industry practices and standards are expected to be in place. For instance, ensuring that the labor force employs the right offering methods of concrete or correctly fits the insulation materials helps in preventing future wear and tear repairs. Thus, the checklist serves as an inclusive tool that aids in maintaining the highest quality of work, accuracy, and safety on the construction site.
Details to Note in Structural Inspections
When conducting structural inspections as part of site progress reviews, a number of key areas warrant a degree of scrutiny often overlooked. Foundation strength, for instance, is pivotal to the overall stability of any structure. A well-constructed and maintained foundation ensures stability and reduces the risk of future structural problems. However, detecting foundational issues is not always an easy task and usually involves looking for signs of uneven settling, cracked or crumbling walls, and water damage.
Masonry and framework are another crucial predictor of a structure’s long-term resilience. Specifically, inspectors should be assessing the brickwork and stonework for cracks, chipping, or loose bricks, as these flaws could ultimately affect the structure’s integrity. Similarly, the inspection of the overall framework takes into consideration the quality and installation of beams, columns, trusses, and floors. Structural deformities, damaged joints, or corrosion are all areas that might flag a need for deeper evaluation or intervention.
Lastly, roofing, an element that often receives less attention than it should during site progress inspections, can be of equal importance. A thorough roofing inspection goes beyond just checking the visible surface. It also involves assessing the associated elements including the chimney, ventilation, flashing, and gutters. Poorly constructed or maintained roofing can lead to problems such as leaks, mould growth, and even structural damage over time. In short, each of these elements – foundation strength, masonry, framework, and roofing – play a critical role in structural integrity and thus require rigorous oversight in site progress inspections.
Monitoring the Construction Timeline and Budget
Progress inspection in construction plays a vital role in managing and monitoring the timeline and budget of the project. Frequently, shifts in these aspects can severely impact the project’s success, causing delays and cost overruns. For instance, an unexpected delay in the delivery of critical materials can disrupt the construction schedule, paving the way for unplanned expenditures. Therefore, timely tracking of the project phase aids in identifying potential issues promptly and enables the project manager to take corrective actions.
One pertinent example is consistent check-ins on the availability and appropriateness of resources, as these have a direct bearing on project timelines and costs. A discrepancy like use of substandard materials not only results in quality issues but also escalates costs due to rework. Invariably, accurate site inspection serves as a keen watchdog to prevent such misalignments between planned and actual expenditures.
Aiding in budget control, routine site progress checks also ensure allotted funds are utilized prudently. For example, inspection reports may reveal unnecessary expenses on redundant equipment or practices—nuances usually left unnoticed but can make a substantial difference to the total spend. It’s akin to the famous quote credited to Lord Kelvin, “If you can’t measure it, you can’t improve it,” underscoring the significance of systematic inspections.
Further, inspections promote accountability among stakeholders by keeping a tight rein on progress in line with the budget. This prevents a lax approach towards economic resource usage, thereby reducing the chances of monetary overspending. Consider how checks on work hour efficiency can reveal wastage of time, that would otherwise go unnoticed until the end-stage project review, reverberating on the total cost.
Moreover, progress inspections play a crucial role in predicting future issues that might arise in the timeline or the budget. By conducting comprehensive inspections and documenting the results, potential setbacks can be foreseen and planned for—saving time, money, and maintaining the sanctity of the project timeline. In essence, site progress inspection works as a predictive tool, identifying lagging indicators before they manifest into substantial issues.
Evaluating Subcontractor’s Work Efficiency
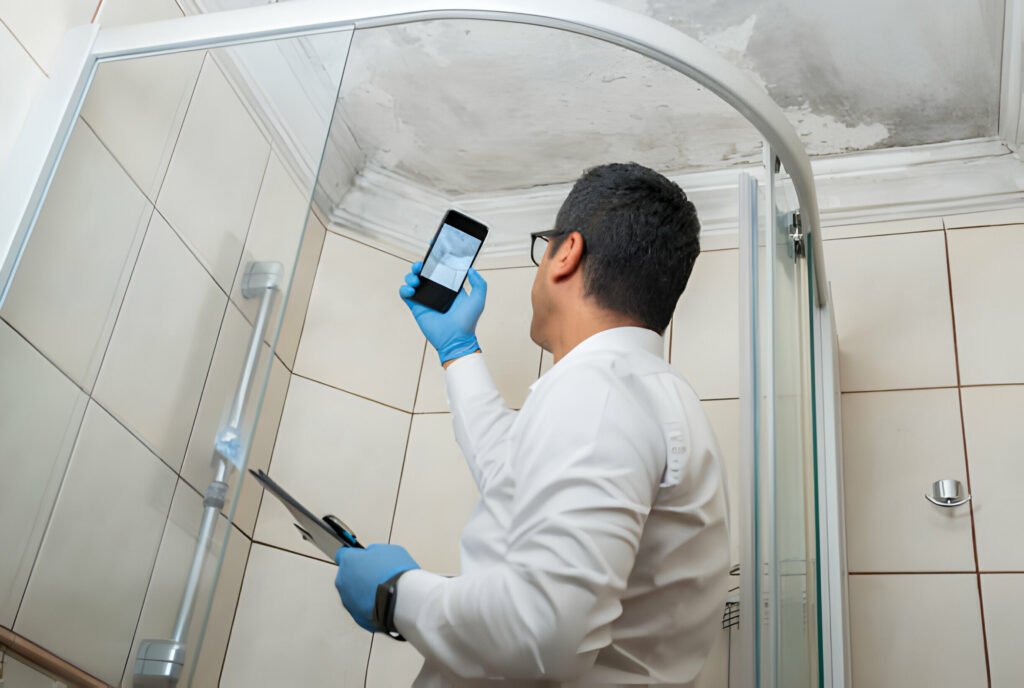
Assessing the efficiency of subcontractors is an essential aspect of site progress inspection. Careful evaluation allows for a transparent understanding of their performance and the value they bring to the project. During this step, the inspector dives deep into the operations of each subcontractor involved, inspecting their methodologies, speed of delivery, technical precision, and commitment to time frames. Factors such as the level of task completion and ability to meet project milestones play a significant part in determining the contractor’s overall efficiency.
We need to look at how deviations in a subcontractor’s efficiency can influence the whole construction project. For instance, a subcontractor completing their work ahead of schedule can accelerate other related tasks, potentially resulting in significant project savings. On the other hand, delays in one subcontractor’s work can lead to a domino effect, causing project timeline extension and cost overruns. Therefore, a project’s success heavily depends on the work efficiency of the subcontractor. This underlines how important it is for site progress inspections to pay close attention to subcontractor performance, enabling the early identification of potential problems and implementing timely solutions. Inspectors can further leverage real-time data and analytical tools to gauge subcontractor’s work efficiency, making the process more transparent and effective.
The Significance of Regular Progress Reports
Inherent to any construction project’s success is comprehensibly establishing the progress and status of work. Regular progress reports play an indispensable role in this process. They offer a snapshot of the ongoing activities on a site, thus aiding considerably in project tracking. Through systematically documented information on the ongoing assignments, potential setbacks, and upcoming plans, managers gain insight to strategize their next moves.
Regular progress reports are not just paper formalities; they are practical monitoring tools integral to project management. They assist in maintaining updated information on a project’s current standing, thus fostering transparency and accountability among team members. For instance, if a certain phase of a project has been completed, it is critical to record and report such progress. This aids in identifying any deviations from the set objectives and the required corrective action, if any, factoring in the contingency plans.
Another important aspect of these reports is that they facilitate detection of inefficiencies at an early stage. For instance, let’s assume that a report reveals extended working hours without significant output; in such a scenario, the management can identify it as a red flag and investigate the reasons for reduced output. Henceforth, the management team can take necessary action, avoiding cost and time overruns, which remain critical in the successful completion of construction projects.
Ultimately, regular progress reports are instrumental in triggering timely decision-making while serving as records for future reference. They help build a healthy communication line among stakeholders. Consequently, project leaders, with the aid of these reports, can provide concrete evidence of the progress for investors. Conclusively, these regular reports embody an effective monitoring mechanism, amplifying the value of site progress inspections.
Software Tools to Aid in Site Progress Inspections
As we draw to a close, it bears stressing how technology plays pivotal roles in simplifying, expediting, and enhancing site progress inspections. With the advent of specialized software tools, conducting thorough inspections have never been easier and more accurate. These applications encompass a broad spectrum of benefits, including streamlined documentation processes, real-time data collection and tracking, and enhanced accuracy in both evaluation and reporting. Notably, such tools align perfectly with the principles of effective site progress inspections, supplementing the objectivity, consistency, and meticulous detail inherent in manual processes. Furthermore, software tools naturally equip construction managers to better monitor the project timeline and budget, as well as evaluate subcontractors’ work efficiency. Indeed, the use of advanced software tools epitomizes today’s embrace of technology in construction project management. It serves as a compelling reminder that advancements in digital solutions continue to empower the industry to reach greater levels of precision and efficiency.
Leave a Reply